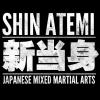
How Bad Is This Lol ?
#46
Posted 30 October 2013 - 09:21 PM
#47
Posted 31 October 2013 - 04:00 PM

At first they were all pigeon poo but then I managed to get a good flow going but none of them penetrated.
I cut a slit with a 1mm girding disc but couldn't get it to go over the gap.
Then I had a go at joining two pieces together which could have gone better lol.The last pic at least shows that I got somewhat of a proper weld as the metal broke and not the weld.
The best results I got were with the gas on 4,power on 1 minimum and wires speed 5.
Ill have another go tomorrow after I read your replies :)
Attached Files
#48
Posted 01 November 2013 - 06:11 PM
What am I doing wrong?
#49
Posted 01 November 2013 - 07:08 PM
Looking at your welds they are getting there but i would recommend the following settings
Try doing tack welds on the slits approx one inch apart then pulse weld in between, these are just a series of slightly stronger tack welds that overlap each other.
The wing metal is a tad too thin to seam weld so get some thicker metal of at least 1.2mm thickness and then try that for seam welding.
#50
Posted 01 November 2013 - 07:54 PM
Had another go today and got a much better looking weld with penetration but as soon as I try and join two pieces together I just blow a hole in the side a start from and can't get he weld to cover the gap.
What am I doing wrong?
You are prob holding the trigger down too long.
As Neil says you need to pulse weld. Hold the trigger down and do one or two circles and stop then repeat.
#51
Posted 01 November 2013 - 09:06 PM
Cheers for the replies :)
#52
Posted 01 November 2013 - 09:07 PM
0.9mm
#53
Posted 01 November 2013 - 10:18 PM
#54
Posted 01 November 2013 - 10:20 PM
No they are fine to weld. I have them fitted to Paddy.
0 user(s) are reading this topic
0 members, 0 guests, 0 anonymous users