Edited by Steve220, 23 December 2014 - 09:32 AM.
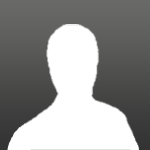
Elliskwleisk - Mk3 Full Nut & Bolt Restoration With Slight Modifications"
#136
Posted 23 December 2014 - 09:32 AM
#137
Posted 24 December 2014 - 11:45 AM
Thanks! I'm sure I'll have an evaluation update at some point in the future, but you may have to wait until April or May! After all this time, money and work, I think it'll be a summer car!I'm interested in seeing how you get on with the H180s and the Philips globes. I have Nightbreakers going into mine and wouldn't mind seeing the difference. Nice going on the carbon floor tray, looks neat :)
Mine will probably be about that time as well, so it'll be nice to compare. Agreed - no point in spending so much effort and money to worry about rust within the first couple of years. That interior looks good!
Sounds like a plan! Where are you located? Appreciate your approval on the interior. It get's better though!
Excellent progress as usual! Friendly bit of advice for mikalor clamps, grease the threads! Otherwise if you have to undo them in a year's time they'll be seized.
Cheers! Ah , I don't know how I forgot to do that! Thank you for reminding me though, I shall do that today!
#138
Posted 24 December 2014 - 12:40 PM
Sounds like a plan! Where are you located? Appreciate your approval on the interior. It get's better though!Mine will probably be about that time as well, so it'll be nice to compare. Agreed - no point in spending so much effort and money to worry about rust within the first couple of years. That interior looks good!Thanks! I'm sure I'll have an evaluation update at some point in the future, but you may have to wait until April or May! After all this time, money and work, I think it'll be a summer car!I'm interested in seeing how you get on with the H180s and the Philips globes. I have Nightbreakers going into mine and wouldn't mind seeing the difference. Nice going on the carbon floor tray, looks neat :)
I'm down in South Africa :) do tell!
#139
Posted 24 December 2014 - 08:48 PM
I'm down in South Africa :) do tell!
Ah! I guess it wont be a parked side by side comparison then! No telling, you'll just have to wait and see!
#140
Posted 24 December 2014 - 10:44 PM
Well I've been spending a lot of time in the garage recently but I'm running out of steam on the whole thing. So I've decided to take some time off of the project and spend some time updating the info on this for all you lovely folks.
Next job was the wiper motor and linkage. I wanted to get this fitted while the engine bay was empty. I purchased a new motor, park swtich, mounting pad, stainless bracket and two new wheel boxes. The rest of the linkage was in good condition so I reconditioned it. I started by stripping down the old motor, removing the gearing, cleaned it all up, fitted it to the new motor and packed it with grease.
I wasn't pleased with the amount of grease it came with, so I packed some more in there and worked it all in. I also purchased a new loom plug but this wasn't required in the end because a new one was supplied fitted to the loom. So I gave it to my local mini pal - Fergus - because his motor was cooked and had melted the park switch and loom plug. Doing my part for the mini community!
So here's all the bits and bobs. I had stripped, cleaned and painted the tubes which carry the linkage earlier.
As a final precaution, I stuck a long piece of stainless steel locking wire down the tube, formed a hook around some strong shop towel and pulled it back through like a pipe cleaner. Worked a treat!
Next job was to clean the actual linkage coil thingy before I fitted it all together. So! I hatched a clever plan! It would take forever to clean just by hand, so I hooked one end up in the drill, soaked it in brake cleaner, stuck some paper towel around it and held it with my hand and then put the drill on full wack in reverse. Cleaned it in seconds! Was spotless after a few goes. Result!
So I got it all pre-assembled on the floor like so. I tightened the wheel boxes on to the tubing just enough that they would stay where they were put, but loose enough that I could rotate them when I had the whole set up in place under the scuttle. I tried the whole offering it up loose, get it in position, take it off and then tighten. But when I offered it back up it was a mile off! So the other method worked a treat.
Next I fitted the motor with a new mounting pad and stainless bracket. I fitted the OE plastic cover later once I cleaned it up.
Job done! I also put the new loom roughly in place through the bulk head.
It was now time to start the time consuming job of wiring. A standard loom just wouldn't do for what I wanted. I wanted so many custom features and various things changed that It was going to have to be a total redesign! So I purchased a full brand new loom for the car to start with as we would use most of its standard features for the engine bay and boot area, but everything in-between is totally custom! One of the big features I wanted is that I wanted the engine bay to appear as "wireless" and "electric gubbins" free as possible. So all the fuses, relays, flasher units, etc have been moved to the electrical board on the back seat. I recruited the help of my uncle - Iain, as he has a lot more knowledge of auto electrics than I do. The two of us struggle to work together at times, well most of the time! But it's almost complete! ... after 4 months Anyway! He arrived from hours and hours away! Months late... With a knackered clutch. So obviously that had to be fixed first. I'm not sure if it was more of a coincidence, or convenient, that it just happened to break as he got to my house, with a car that has to have the engine removed to change the clutch, and I have an engine crane...
But anyway, I was chomping at the bit and was being impatient but he had to get it done.
So while that was going on, I decided to start bolting some bits and pieces on to the engine while it was on the bench. Started off with these bad boy triple electrode plugs, supplied in the Accuspark electronic ignition kit.
Then I did the flywheel side bits and bobs.
I also stripped the flywheel housing because it was a mess! So got that all cleaned up and the end put together with a new genuine slave cylinder, bunch of stainless bits from Smiffy, subframe mount, plunger and arm, retro sport cap head bolt kit, thrust release bearing etc.
I then rotated it and fitted the retro sport oil filter housing and pipe. Oil pressure adaptor, alloy, so wont corrode like the crappy zinc coated ones! So that will be connected to the oil pressure gauge stainless pipe as well as the already connected 20PSI low oil pressure light. I believe the standard one is set at 5PSI to bring the light on, but as minispares says, that's far too low to prevent damage. I also fitted a new oil pressure relief valve kit and adjuster. Along with a new temperature sender and more stainless smiffys bits. Everything has been sealed with the Wurth Anaerobic sealant - Top stuff!
I then got my radiator set up roughly assembled to offer it up and check clearance on the fan. I have fitted it with Minispares silicone hoses, electric fan switch in the base, an over flow hose secured by a stainless P clip, DSN retro sport alloy hose joiner and Mikalor clamps to connect the hoses, where clearance allowed. I also replaced the fan because I felt this old beauty had met its time to retire.
Nice and clean inside!
Wee night shot!
So after that, I fitted the lower dash rail and got the rest of the standard loom sprawled about the place for Iain.
On a different note, I ordered some exposed weave carbon fibre arches from The Arc Angels. After waiting almost two months, I was more than disappointed because the finish was crap! And they fitted like a dogs dinner. They were wafer thin and flimsy too. I was so angry that I just stuck them back in the packaging and sent them back so I've only got a photo of them in the plastic. But it's safe to say, after the front end, boot lid and those arches, I wont be using them again! On top of that, it took them about two months to refund me!!! Absolute joke.
So the type of arches I want, pictured below, I saw on an arches thread, but obviously they aren't sold anymore. So I'll have to sort something else out.
I also decided that because the paint job and front end fit is so poor, in my eyes, that I would purchase a pair of these wheel arch liners to try and prolong its life as much as possible. But I think I've done enough moaning about businesses already today, Simons in Darlington is a wholeeeee different story now that I've spent a lot more time with the car and seen every angle of it.
Then I decided to pull a bunch of parts out that I needed painted or that I wasn't happy with the factory finish, like these additional engine stabiliser kits and all the heater parts, and send them off to Hendersons metal cleaning in Edinburgh to get blasted and painted in a more durable finish.
While all this was under way, I was doing some work for a family friend who has quite the collection of classic cars. Here's a photo, of a photo on his wall of a fully aluminium, supercharged, Downton MK1 Cooper he used to own and rally! Sadly, it was stolen a number of years ago.
Edited by Elliskwleisk, 24 December 2014 - 10:58 PM.
#141
Posted 24 December 2014 - 10:45 PM
I also got my hands on a set of good nick MK4 onwards, rear opening windows, thinking I could swap the catch and slap em in! Well, I was wrong. the catch is completely different and where it attaches to the window is completely different. I then decided to strip one of my windows and get the catch piece that is corroded and the hinges, remade at the engineers shop in stainless steel. But as I stripped it apart I decided that this was way too much work. I may eventually go down this route but for now, I'm still on the hunt for a mint set.
Next little job was to clean up the stainless subframe lock tabs and the excess wax on the bulkhead and inner wings. I had sprayed waxoyl around the tabs but it was messy. So I injected wax inside them and all around them, cleaned it up, masked it off and sealed it with tiger seal. Can't have water in the cross member!
I haven't got a finished photo of that ^ for some reason. Its nice and neat now though.
Then I got all the parts back from hendersons. Beautiful job done, once again! Honestly, other than John - who helped me with the engine, Hendersons is the only place that I have used during this project that I would actually recommend. Anyway, really good strong, durable and thick finish! Ace.
So while watching TV one night I decided to assemble most of the heater box with some lovely stainless steel flanged headed screws. So I got all the parts together, tested the motor out and cleaned it and began assembling.
I decided that I would properly flush out the matrix and make sure it was okay but it was a bit spluttery.
Anyway, then I decided to try and dry it out so I left it on the front step with B&Q's finest hot air gun on it to dry it out. Keith wasn't too pleased and said "Make sure it doesn't go on fire!", which I replied with "Yeahhh, it'll be fine..." Went out two minutes later and it was smouldering away!
All the brazing had melted and ran away, leaving the inlet buggered!
So I had to order a new one.
So once it arrived, I got it all stuck together. In hindsight, I'm quite glad because apart from the block and cylinder head, all the other cooling system components are new.
No finished photo of that either yet. Slackin!
Iain has been hard at work routing the cables along the roof gussets. on the passenger side he has ran two thirteen core cables and fitted multi blocks at either end. like triple the amount of cable running to the rear already!
Then we decided to test fit the engine so that I could mark out where I wanted to fit the solenoid, fuel pump, air horns, etc.
So up it went!
And in it went!
I also fitted a new thermostat and a Smiffy stainless twin hole plate to the N/S of the cross member. Sealed with the Butyl strip.
It was depressing offering the engine in and then taking it out again. But Iain was right, it was the right thing and the easier way to do things so he eventually persuaded me. So out it came and I got on with drilling mounting holes.
Got them all drilled and painted up. We also got the battery cable and the fuel pipe secured better where it'll rub on absolutely nothing. Result! We also ran a high heat resistant tube down the length of the fuel pipe that is within eight inches of the exhaust manifold.
Followed by stainless steel rivnuts in all the required holes.
I also noticed another late night job I had done. The banjo bolt for the O/S brake calliper flexi was too long for some reason. I even bought a new one which was too long. So I had decided to just double washer it!!!! So that HAD to go.
Out it came, in the vice, trimmed down, filed smooth, swarf removed and stuck back in with a new washer and no issues!
Anyway, the day arrived, FINALLY! Time for my "half of a V8" powerhouse, to be slotted back in.
So in she went! With plenty wing protection of course.
First job was to get it properly mounted and as usual in the mini world, it didn't fit. I tried liberal amounts of grease, pry bars, jumping on it, shuffling the mounts, you name it! So I did some research and I had heard about someone using a big G clamp. No idea what size or shape because everyone is first to throw a bright idea out there, but forgets to add the essential information! So on to eBay I went, came across this big, second hand 8" Record G Clamp for a tenner and took a gamble.
It arrived a few days later. Armed with G clamp and wood, I closed up the garage doors and went at it!
I took several poor quality, bad angled photo's, but hopefully anyone interested and having the same problem will be able to understand. I put the adjusting end on top of the engine mount, and running the main body of the clamp on the inside of the subframe past the speedo drive housing, It slid under the subframe. I used the piece of wood to protect the paint.
I know it's hard to understand and see, but it works a treat! I just tightened the clamp by hand and it slid right down no bother! So anyone wanting more info on this, feel free to ask.
After that, I got on with the top engine steady to give it some stability. DSN retro sport billet alloy of course, with new bushes pressed in in the vice.
Anyway, that'll do for a Christmas Eve update I think. Merry Christmas Everyone.
Edited by Elliskwleisk, 24 December 2014 - 11:08 PM.
#142
Posted 24 December 2014 - 11:07 PM
Very good update mate!
It's coming on well.
Merry xmas to you too!
Ben
#143
Posted 24 December 2014 - 11:22 PM
Awesome build this. Thanks for your replies and all the detailed pics - they have helped me a lot.
Merry Christmas
Pete
#144
Posted 24 December 2014 - 11:40 PM
Love it, as others have said the attention to detail is epic! Also, I started out wanting reverse rims for my project but decided they wernt wide enough, and have never been sure about the quality of banded steels - however yours look superbly done! Would you mind telling me who did them, and the exact specs of them, as the poke on your set looks perfect to fill my arches. Cheers!
#145
Posted 25 December 2014 - 12:19 AM
Very good update mate!
It's coming on well.
Merry xmas to you too!
Ben
Awesome build this. Thanks for your replies and all the detailed pics - they have helped me a lot.
Merry Christmas
Pete
Love it, as others have said the attention to detail is epic! Also, I started out wanting reverse rims for my project but decided they wernt wide enough, and have never been sure about the quality of banded steels - however yours look superbly done! Would you mind telling me who did them, and the exact specs of them, as the poke on your set looks perfect to fill my arches. Cheers!
Thanks for all your replies chaps!
Pete - I am slowly making my way through your build thread. I wish I could go back and put the amount of effort and attention in to my body work as you have! I'm sure I'll regret it some day. Any other questions, do not hesitate to ask.
Miniman - The wheels are "Marmite", as people say. But I don't care. I absolutely love them! One negative is that everytime you remove the hub cap, it gets slightly deformed, but more annoyingly, the wheel gets chipped, every time. All my wheels need painted again.

http://www.bandedsteelwheels.co.uk/
The only part I wasn't pleased with was the powder coat finish that they did. It wasn't up to my picky standards.

Hope this helps folks.
Edited by Elliskwleisk, 26 December 2014 - 01:10 PM.
#146
Posted 25 December 2014 - 12:23 AM
Excellent, thanks for the info :) Im running 7.5" discs and spacered drums too - my arches are the Wood and Picket type (seen in my sig) and my current 10x5 Mambas fill them perfectly - the Mambas have a rather large offset though, and are not "deep" enough looking for me anymore. I will go for the 10x6 band and add spacers as necessary :) Following thread, look forward to updates!
#147
Posted 26 December 2014 - 10:28 AM
I'm down in South Africa :) do tell!
Ah! I guess it wont be a parked side by side comparison then!
No telling, you'll just have to wait and see!
Probably not
#148
Posted 26 December 2014 - 11:35 AM
Edited by GraemeC, 26 December 2014 - 11:36 AM.
#149
Posted 26 December 2014 - 01:17 PM
Is there a copper washer under that banjo fitting as well as on top? If I remember right they are different sizes top and bottom.
You are correct, yes. There is one copper washer between the banjo bolt head and the hose banjo and a smaller copper washer between the underside of the hose banjo and the flexi pipe connector. The only thing that crossed my mind is that the stainless steel flexi pipe female connector may not be as deep as the standard item.
The only other problem that I am having that I wondered if anyone could help me out with is that my handbrake cables are rubbing on the exhaust tunnel. Here's a link to the thread about it:
http://www.theminifo...-touching-body/
Any help or ideas would be greatly appreciated as I am completely stumped!
#150
Posted 26 December 2014 - 03:43 PM
Here are some photos of the problem:
So I removed the bottom plate and pad because in the haynes manual and on the diagrams on minispares etc, it only shows a top one fitted. But that didn't make a difference either.
So I then trimmed the bottom plate slightly and inverted it. This stops the cable rubbing on the tunnel but I imagine it will eventually just chew right through the fair lead plate because it is only soft metal? I am also concerned that the cable is now rubbing on the front side of the slot cut in the tunnel that the cable runs through.
Any other ideas?
2 user(s) are reading this topic
0 members, 2 guests, 0 anonymous users