Just a query similar to this thread, I too neglected to remove oil gallery plugs in rebuilding, although I did clean entire block after reboring, i.e . washed out with engine degreaser then pressure washed it and finally ran a high pressure air line through all the orifices etc. My question is can the plugs be removed still at this stage ( have the crank,pistons,cam and timing gear in now) ? Once the plugs are out and the galleries cleaned then to blow the pipes clean would mean that any left over muck would be pushed further into the engine wouldn't it ? Ferg
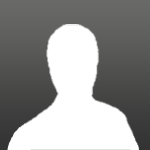
Replacing Oil Gallery Plugs
#16
Posted 02 January 2016 - 03:52 PM
#17
Posted 02 January 2016 - 05:09 PM
1. The oil galleries MUST be thoroughly cleaned during any engine re-build.
2.. The crankshaft MUST NOT be installed during the gallery cleaning process or DGS will get between the bearing shells & the crank journals
3. The oil pump and oil pressure relief valve MUST NOT be fitted at this stage either. In fact the block needs to be completely stripped.
#18
Posted 02 January 2016 - 06:39 PM
How many oil core plugs on the 1970's 1275 gt
#19
Posted 03 January 2016 - 02:10 AM
How many oil core plugs on the 1970's 1275 gt
7 in total;-
2 in the Mail Oil Gallery - 1/2"
2 in the Return across the tops of the Cam Followers - these are not in the Pressure Circuit - also 1/2"
2 for the Oil Pressure Relief Valve - 1/4" from memory so don't quote me on them
1 in the cylinder head also 1/4"
#20
Posted 03 January 2016 - 08:51 AM
The oil gallery blanking plug holes can also be drilled and tapped to enable a suitable plug to be fitted.
#21
Posted 03 January 2016 - 09:36 AM
#22
Posted 08 August 2020 - 04:10 AM
I normally use a 1/2" drill to get the old gallery plugs out, then thoroughly clean the galleries and re-fit using a bit of Loctite Bearing Seal.
So you drill into them. Then what? How do they come out?
#23
Posted 08 August 2020 - 08:50 AM
I normally use a 1/2" drill to get the old gallery plugs out, then thoroughly clean the galleries and re-fit using a bit of Loctite Bearing Seal.
So you drill into them. Then what? How do they come out?
I always fear damage to the existing drilling in the block, by going in with a drill of the same (or close to) again. I drill a small hole (6.8 mm) then tap that 5/16" UNF for my slide hammer. This is for the early, solid brass plugs. The later pressed type plugs, I punch a hole in and screw a Self Drilling Roofing Screw in to, that also fits the Slide Hammer.
I only get one out this way, then drop a short length (about 15") of 8 mm rod through the gallery and knock the other one out.
Each to their own, and if you're comfortable to drill them, then there's nothing wrong with that either. It would be faster than my approach.
#24
Posted 13 August 2020 - 07:02 PM
So you drill into them. Then what? How do they come out?I normally use a 1/2" drill to get the old gallery plugs out, then thoroughly clean the galleries and re-fit using a bit of Loctite Bearing Seal.
I always fear damage to the existing drilling in the block, by going in with a drill of the same (or close to) again. I drill a small hole (6.8 mm) then tap that 5/16" UNF for my slide hammer. This is for the early, solid brass plugs. The later pressed type plugs, I punch a hole in and screw a Self Drilling Roofing Screw in to, that also fits the Slide Hammer.
I only get one out this way, then drop a short length (about 15") of 8 mm rod through the gallery and knock the other one out.
Each to their own, and if you're comfortable to drill them, then there's nothing wrong with that either. It would be faster than my approach.
Thank you for the info!
Still, whats the full approach for drilling them out? Once you drill a hole in it won’t it still be inside?
#25
Posted 13 August 2020 - 07:38 PM
Thank you for the info!
Still, whats the full approach for drilling them out? Once you drill a hole in it won’t it still be inside?
I'll let the Pictures do most of the talking;-
I do find the Brass Plugs easier to drill if you put a small Pilot Hole in first
Then Drill to Tapping size (6.9 mm here)
Tap 5/16" UNF
Screw in the Slide Hammer
A Gentle Tap
and out it comes
Shove a length of 8 mm Rod through
A couple of taps on the Rod
and that's the other end out
#26
Posted 13 August 2020 - 08:16 PM
Thank you for the info!
Still, whats the full approach for drilling them out? Once you drill a hole in it won’t it still be inside?
I'll let the Pictures do most of the talking;-
I do find the Brass Plugs easier to drill if you put a small Pilot Hole in first
Then Drill to Tapping size (6.9 mm here)
Tap 5/16" UNF
Screw in the Slide Hammer
A Gentle Tap
and out it comes
Shove a length of 8 mm Rod through
A couple of taps on the Rod
and that's the other end out
I understood your instructions but I thought cooperman was implying that he simply just drilled into them and that was it. That’s what I was confused about. Again thank you
#27
Posted 13 August 2020 - 09:52 PM
I thought you were referring to the newer pressed and dished plugs. I find that if you drill them with a 12 mm dia drill, they just come out sort-of stuck to the drill bit without damaging the bore.
Then clean up the hole and fit the new ones with a bit of Loctite Bearing Lock (from memory as it's too late to go out to my workshop, it's Loctite 271) I've never had one leak or come out under even high oil pressure.
#28
Posted 14 August 2020 - 06:48 AM
I thought you were referring to the newer pressed and dished plugs. I find that if you drill them with a 12 mm dia drill, they just come out sort-of stuck to the drill bit without damaging the bore.
Then clean up the hole and fit the new ones with a bit of Loctite Bearing Lock (from memory as it's too late to go out to my workshop, it's Loctite 271) I've never had one leak or come out under even high oil pressure.
Yep should be the newer type as it’s from a 1992 1275 A+
So do you drill in then reverse the direction of drill to pull them out?
#29
Posted 14 August 2020 - 07:01 AM
Or would a 15/32 work better which is slightly under 12mm?
https://www.homedepo...-4627/205879021
#30
Posted 14 August 2020 - 07:14 AM
1/2" is the hole size the plug fits in to - I wouldn't risk that as if you mark the original bore there's a chance the new plug will either not seal or could get pushed out later.
Try the 15/32" - if it doesn't grab the cup and spin it as per Cooperman's explanation then it will at least a very thin wall which could easily be folded in on itself to remove.
1 user(s) are reading this topic
0 members, 1 guests, 0 anonymous users