Do you use just a flap disc to grind welds down?
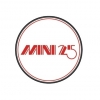
Three Classics. One Passion.
#31
Posted 22 December 2014 - 11:06 AM
#32
Posted 22 December 2014 - 11:26 AM
Keep it up very tidy
Edited by MINIMADrt, 22 December 2014 - 11:27 AM.
#33
Posted 22 December 2014 - 04:58 PM
#34
Posted 22 December 2014 - 05:06 PM
Thanks. Ben I used a flap disc yes. It was difficult to keep off the panel while grinding down the welds. It was a tight curved angle to get in. Any suggestions ?
Use the edge of a grinding stone or a 4mm cutting disc to get the bulk of the weld down and only use a flap disc for smoothing the weld out if you need to after using the stone.
Using only a flap disc (which are quite expensive) will mean you will get through loads of them and like you found, you will run the risk of getting the panel to hot and warping or thinning the metal out too much.
a stone is cheap as chips and under normal use will last a long time.
Ben
#35
Posted 22 December 2014 - 05:09 PM
If you look about half way down this page, you will see what i mean.
http://www.theminifo...rebuild/page-32
You have much more control with a stone and if you really take your time (i.e don't lean on the grinder) then you can keep the stone on ONLY the weld and not the surrounding metal.
Hope this helps.
Ben
#36
Posted 22 December 2014 - 08:40 PM
#37
Posted 22 December 2014 - 08:48 PM
Yes I should have thought of that thanks Ben. Ive got a few stones so I'll try them next. Cheers for the top tip.
That's ok, I find them better when they are about half worn.
I try to keep a 4mm cutting disc and a stone half worn as well as unworn ones. That way, you can use the larger unworn discs in easy to reach open areas and the smaller half worn discs are good for tight spots.
I usually start off with the stone to get the bulk down, then switch to the 4mm cutting disc to take it right down level like in the pictures i linked you to in my thread and then buzz over with a coarse flap disc to take out any deep stone marks left behind.
Takes time but worth it in the results.
I might buy a second grinder so i can leave a disc in each to speed the process up..
#38
Posted 22 December 2014 - 10:44 PM
Looking good Stu...
#39
Posted 22 December 2014 - 11:42 PM
#40
Posted 24 December 2014 - 02:54 PM
Got some shaped stones in case I need to get to hard to reach areas when grinding down welds. Hopefully they'll come in useful.
I got my panels from M Machine, so I set about removing the passenger floor pan.
It took some getting out due to all the patch plates, but got there in the end.
Lots of spot welds in the front lip to drill out.
Spot welds ground down to bulkhead lip.
I think I'll need to remove the inner wing next to allow me to fit the floor pan and new inner wing which I've not got yet. Removing the inner wing and preparing the metal ready for the new panels will take a while so theres no rush. Once I've got them in I'll move to replace the inner and outer sill.
All for now. Merry Christmas everyone
#41
Posted 27 December 2014 - 09:51 PM
I started to poke aroud the front passenger inner wing to see what was underneath the cover plates. This is the inner arch repair panel. It's been welded over the top of the original inner wing. I peeled it back at the floor / sill to see whats underrneath.

So I decided to dig a bit more and took the entire repair panel off.


To be fair the original inner wing in this area is still fairly good. The holes at the base could have been repaired with localised infill, so it seems odd to have slapped a full height panel on.
I decided that I'd have to cut out about 70% of the panel to repair it, and thought it'd be easier just to replace the whole inner wing, so I went about cutting it all out which was a good job as there was a lot of corrosion around the shock mount which was covered up by the panel repair plate.

I still have a bit to remove at the top and up the a post closing panel but most of it's out.


I'll need to spend some time cleaning up the flanges before looking to fit the new floor and inner wing.
Edited by Stu., 19 April 2015 - 07:16 PM.
#42
Posted 30 December 2014 - 12:00 PM
Ive always liked the deep blue colour of the old Austin 7's but it's a little too purple for what I want on Felix so I've chosen Mineral Blue BU9 which I think was used on MG's rather than Mini's.


Wonder how long it'll be before putting some through the gun ?
Edited by Stu., 30 December 2014 - 12:05 PM.
#43
Posted 03 January 2015 - 09:14 PM

New plate in place.

Welded up and zinc primed.


That's all I got done today. I've been using 0.8mm wig wire but tried out 0.6mm, but I found it difficult to weld with as I've been used to 0.8, so I'll probarbly stick with it for now.
I've decided I need a welding trolly as I'm fed up with dragging all the gear around and worrying about the bottle falling over and breaking the regulator gauges. I've got a VAT free day card for Machine Mart for tomorrow, so I'm off there to get one & save 20%.
Edited by Stu., 19 April 2015 - 07:20 PM.
#44
Posted 03 January 2015 - 09:35 PM
I've decided I need a welding trolly as I'm fed up with dragging all the gear around and worrying about the bottle falling over and breaking the regulator gauges. I've got a VAT free day card for Machine Mart for tomorrow, so I'm off there to get one & save 20%
Don't buy one!
They are very simple and cheap to make. You will save loads making one yourself and you can customise it to carry all of your welding gear.
I made one and am really pleased with it.
#45
Posted 03 January 2015 - 09:56 PM
2 user(s) are reading this topic
0 members, 2 guests, 0 anonymous users