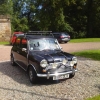
Boot Repair Help
#16
Posted 08 January 2015 - 02:01 PM
#17
Posted 08 January 2015 - 02:02 PM
It is a real shame. That area is just a massive water, mud and salt trap. Not really much you can do as they are crucial to the rear subframe support.
Bloody Mini's!!
what about aluminium panels? not for this job mind, just thinking in general. and carbon fibre/fibre glass valance?
#18
Posted 08 January 2015 - 02:02 PM
The one thing you could to the close out is to enlarge the drainage on them.
didnt realise there was drainage on them?
#19
Posted 08 January 2015 - 02:05 PM
There should be a drainage hole on the bottom of the closing panels. Neil's suggestion about enlarging them is a good one and might help.
I don't know how successful you would be with fitting a composite valance though. I am surprised that they are rusting out so quickly for you though.
What do you do about prep when fitting the valance? Also what types of primer and wax do you use?
Ben
#20
Posted 08 January 2015 - 02:16 PM
There should be a drainage hole on the bottom of the closing panels. Neil's suggestion about enlarging them is a good one and might help.
I don't know how successful you would be with fitting a composite valance though. I am surprised that they are rusting out so quickly for you though.
What do you do about prep when fitting the valance? Also what types of primer and wax do you use?
Ben
I never noticed! will have a look when my new ones come!
I never fitted the last valance, it was my mini mechanic (top work!). The only think i can comment on is the underseal/wax i use! i use tetrasyl (dont hoink thats how you spell it) for all the undeside and waxoil for all the cavities.
#21
Posted 08 January 2015 - 02:26 PM
It might be worth finding out what type of primer is used on the bare flanges and how thoroughly the sealing up has been done afterwards.
Any gaps or poor adhesion of the sealant will let water/muck in and rot it out behind the sealer.
#22
Posted 08 January 2015 - 02:32 PM
I tend to use U-POL etch and weld through primer, as well as stripe seam sealer (the brushable stuff from a tin)?
#23
Posted 08 January 2015 - 03:20 PM
If you don't clean off the burnt paint then whatever you apply over it will not adhere. I know where it's not possible to get to the back of the welded area I try and flood as much paint in as possible then followed by Dinitrol / Waxoyl etc. even if you have to drill a small hole to force the products in then you can fit a grommet into the hole.
#24
Posted 08 January 2015 - 03:37 PM
The biggest thing to remember when using zinc rich primer is after welding has taken place where possible you need to get some scotch brite or similar to clean up the burnt paint. Then etch prime but make sure it's flashed off properly before adding seam sealer.
If you don't clean off the burnt paint then whatever you apply over it will not adhere. I know where it's not possible to get to the back of the welded area I try and flood as much paint in as possible then followed by Dinitrol / Waxoyl etc. even if you have to drill a small hole to force the products in then you can fit a grommet into the hole.
Noted! Will try and remember that. good plan about drilling a hole to get the waxoil in!
#25
Posted 08 January 2015 - 03:40 PM
The biggest thing to remember when using zinc rich primer is after welding has taken place where possible you need to get some scotch brite or similar to clean up the burnt paint. Then etch prime but make sure it's flashed off properly before adding seam sealer.
If you don't clean off the burnt paint then whatever you apply over it will not adhere. I know where it's not possible to get to the back of the welded area I try and flood as much paint in as possible then followed by Dinitrol / Waxoyl etc. even if you have to drill a small hole to force the products in then you can fit a grommet into the hole.Noted! Will try and remember that. good plan about drilling a hole to get the waxoil in!
First job i had when i left school was working for a company called Rust protection. Drilling holes in new cars was a tad daunting.
#26
Posted 12 January 2015 - 10:00 AM
- i used a spot weld cutter to separate the panel, and now left with holes in the rear panel lip, do i weld these up before continuing, or should i use these to plug weld the boot floor (they're pretty sproadic)?
- because i need to weld the boot floor and valance, do i plug weld the rear panel to boot, then drill holes in that to plug weld to the valance, or can you plug weld all three panels together?
- whats the best way to weld the repair panel to the boot floor?
cheers :)
Edited by finch661, 12 January 2015 - 04:07 PM.
#27
Posted 12 January 2015 - 07:01 PM
I would just use the holes that you have already drilled, you can always drill a few more. Weld the boot floor to rear panel lip. Then drill holes in the valance and weld that to the boot floor.
#28
Posted 12 January 2015 - 10:14 PM
#29
Posted 13 January 2015 - 07:35 AM
ah cool :) thats what I thought :) for the the repair to boot floor, is it best to leave an over lap or just seam weld it?
Best bet is to butt weld it. but of you do overlap it, make sure you get plenty of zinc primer in there and seal it up thoroughly or you will end up with a rust trap
1 user(s) are reading this topic
0 members, 1 guests, 0 anonymous users