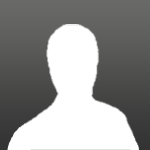
Anyone Using Magnets Around Their Oil Filter?
#46
Posted 04 November 2016 - 07:58 AM
#47
Posted 04 November 2016 - 09:35 PM
Sledgehammer, good try but sorry but I have to respectfully disagree because the nature of a dipstick and it's fitment to the engine is such that much of the crud will be scraped off and fall back into the transmission case every time you check the oil. A sump plug comes out cleanly with little tendency to dislodge muck, and if any does drop it is in an accessible place. It is feasible to put a long magnet in there while the plug is out and retrieve whatever is lying on the bottom, but I have never heard of anyone doing it.
Anyway iron particles are about 8 times as dense as oil so where are most going to be trapped? Not at dipstick height but right at the bottom of the casing, which is where a drain plug needs to be. Alec did not miss that happy juxtaposition.
Maybe you could think up a way of trapping particles over the entire bottom of the casing, perhaps with a large multiple magnet? If you could migrate them to the drain hole when required, you would then have a real winner.
#48
Posted 04 November 2016 - 11:32 PM
the sump plug is without doubt the best way - as you say gravity , makes that position an easy place to collect muck
but is only changed once a year / 3000 - 6000 miles
these engines / gear boxes will be making more particles than 20 years ago so we do need a way to get more particles out
I wonder if there is a way of getting to the bottom of the strainer from the oil drain hole
with a bent rod with a small magnet firmly attached , when changing the oil ?
or even just scavaging the bottom of the gear box from there
also jacking the car up on the near side helps drain more oil out
Edited by sledgehammer, 04 November 2016 - 11:44 PM.
#49
Posted 05 November 2016 - 10:07 AM
ive changed my oil 12 times in 23000 miles since rebuild and havent seen any particles hardly on the sump plug
and no metal bits left in the bottom after oil has been transfered to an old oil can
however i will get one of those minispares drain plugs
i used to run a wrap around magnet on oil filter on my suzuki swift GTI in AUS
did 190,000 km and was still going strong so doesnt seem harmful
#50
Posted 05 November 2016 - 07:01 PM
Or, convert to seperate lubrication for engine and transmission. I believe it has been done, but don't know if you can buy the system or have to do it all yourself. Obviously machining is involved, the engine part needs to be dry sumped with a collecting tray above the gearbox, and special arrangements have to be made at the clutch end of the crankshaft etc. And the has to be some way of checking both levels independently so that a leaky seal does not allow one system to drain completely into the other. But it would keep gearbox swarf well away from engine bearings, which is the main reason for the magnets.
Something for someone with too much time and a modicum of money to attempt perhaps? The ultimate A series engine? Chain drive too, or reversed rotation and no idler gear. 7 or 8 port crossflow head. Modern cylinder liners, bearing shells and crankshaft machining. Good for upwards of 200k miles in a normal state of tune? I would love the job of life testing it on the road...
But mucking out the oil, grot and gunge, as you suggested, regularly will be a lot cheaper, and viable for most of us.
#51
Posted 05 November 2016 - 10:39 PM
The use of a stronger magnet will make surprisingly little difference. But a longer magnet will be useful, provided that there is clearance for it to be fitted.
If you want to make something better, which as far as I know can't be bought off the shelf for a car, get some short hollow tubular magnets and stack them on a non-magnetic rod (many types of stainless will do, or ali or brass). You need to face them so that they are repelling each other, not attracting. Fit the stack to the drain plug in the usual way, but be very sure that it can't unscrew! That way you get an external pole at each interface between opposing poles so you have a series of crud-collecting poles, not just the one at the end. I have seen such a thing, not in a car engine, but am not allowed to tell you where. Or, I will be on a long visit to one of Her Majesty's less salubrious premises.
Oh, and boron based magnets will be cheaper and more powerful than neodymium, although quite frankly plain old alnico will pick up crud efficiently.
I can't find 'Boron' magnets as you say but I've just done some homework and it appears that Neodymium magnets are more commonly known as Neodymium Iron Boron ("Neo", NdFeB or Neodymium)I'm not sure but I think the two are the same and not individual items, anyway 'Neo magnets' are real cheap on EBay and in abundance in various quantities, It is said that these are one of the most strongest magnets developed in 1982 by General Motors and Sumitomo Special Metals (part of the Hitachi Corporation, apparently Chinese manufacturers have become a dominant force in neodymium magnet production, based on their control of much of the world's sources of rare earth mines so I think I'll buy some of these.
I've just found magnets on EBay with the hole in, very cheap also in abundance, thank you.
I would imagine you would be using this kind of technology on hydraulic antiskid braking on aircraft, don't worry your secret is safe with us.
Edited by neal, 05 November 2016 - 10:48 PM.
#52
Posted 06 November 2016 - 05:42 PM
Sorry, I was confused. Been a while since I bought any magnets and I got the Neodymium and Boron separated in my mind. I had the feeling that it was something like Aluminium Iron Boron, with some carbon too, And yes, they are cheap!
We did use powerful magnets in the antiskid systems but they were the older and fiendishly expensive Samarium Cobalt, which has the advantage of a higher Curie temperature. They were only in the electrohydraulic servo valves (Google "Moog Valve"), marvellous devices by which a very small electric current can control a mighty hydraulic ram with great speed and precision. Only in a pumped system of course. I was looking at these for my idea of redesigning the rear braking of the Mini to have proper load-sensing proportioning, but it turned out that they are about £2200 each on Ebay. Last time I bought some at work for a project, maybe in 1988, they were about £450 each. So that idea died, but I have maybe found a source of electrohydraulic actuators, basically a NdFeB brushless torque motor driving a conventional master cylinder via a recirculating ball screw, which will do the job in a conventional hydrostatic system. I was going to think about designing something myself, as I am familiar with torque motors, ball screws and obviously master cylinders, but it seems to have been done already, in a neatly integrated unit. The clumsy but doable way of course is to use vacuum solenoid valves, quite inexpensive, to control a slightly modified vacuum brake servo. Maybe I will have something more to say about this in about 2 years...
It was something quite different that I can't tell you about! I suspect that copies of aircraft maintenance manuals are moderately easy to come by and reveal quite a lot.
1 user(s) are reading this topic
0 members, 1 guests, 0 anonymous users