Hello again. Is any one watching this or is the footy on Ha Ha.
Any way here are the pictures of the diff strip. Even if it is only me.
First I used the bearing pullers thinking the bearing would just pop off in one piece. Got a bit of a shock when the outer race came off and left all the balls and bits still on the shaft,
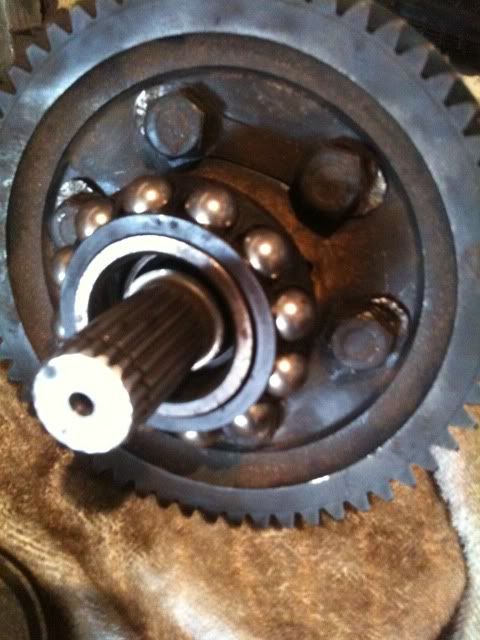
So i pulled off the ball cage by hand.
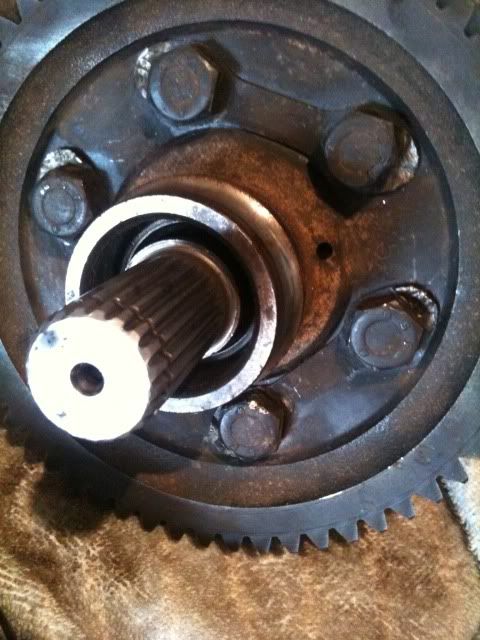
And then used the pullers again to remove the inner race.
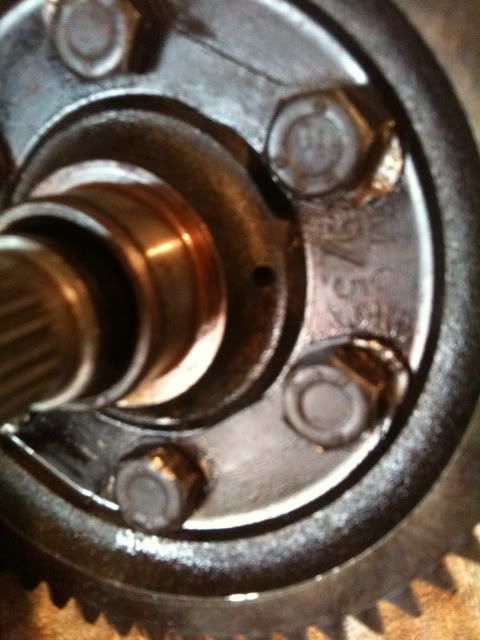
Now I thought id broken the bearings and was about to order new when guessworks told me thats what happens with these bearings and not to worry because they go back together with a sharp tap of the persuader.
Next job was to get the crown wheel off and let me tell you those bolts are torqued to "F" tight. Clamped the cog in the vice and got the long bar on to it.
You can see from the picture that I had already opened the tab washers.
Here it is with the crown wheel off.
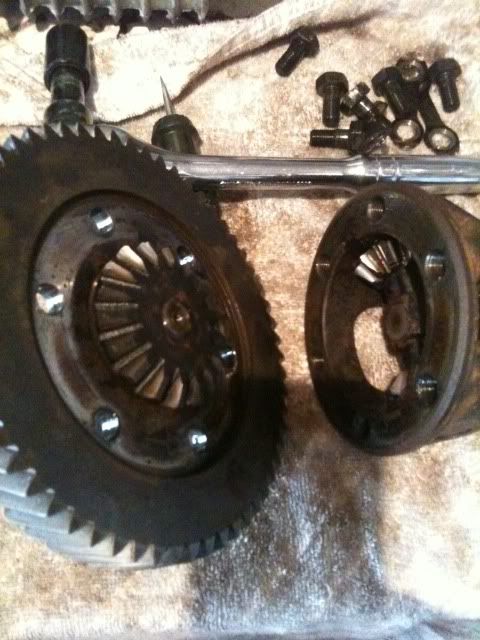
The long spindle cog thing (sorry dont know its name) Will now pull out of the crown wheel, but dont loose the big plasticy washer, you might need it when rebuilding, Ive heard the new ones that come in the rebuild kits are a tiny bit thicker.

This next picture is the roll pin which holds the diff pin in the cage, This is also in very tight but with a few spirited blows with the hammer it started to come out.
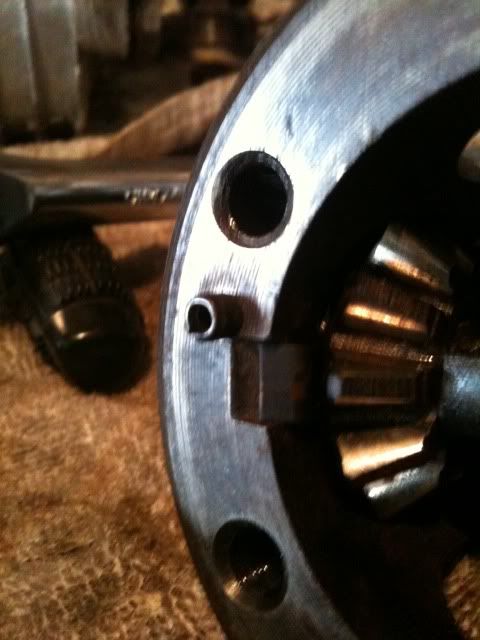
Once you get it out you can tap out the diff pin you can see the groove in the diff pin where the roll pin sits.
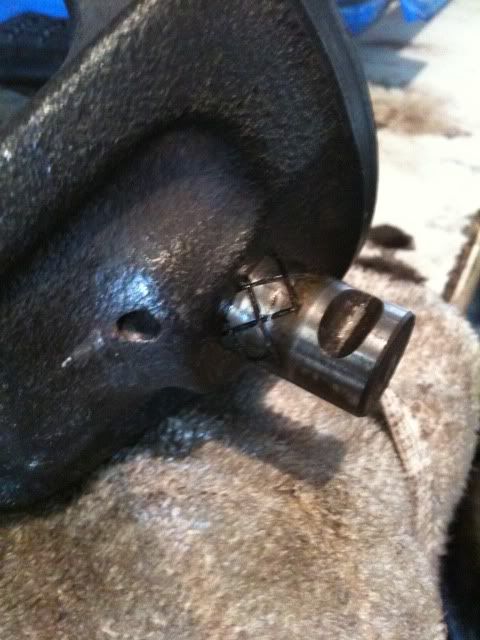
With the diff pin out all the other bits just kinda fall out, the small cogs and copper looking shells. and thats it stripped. All the bits.
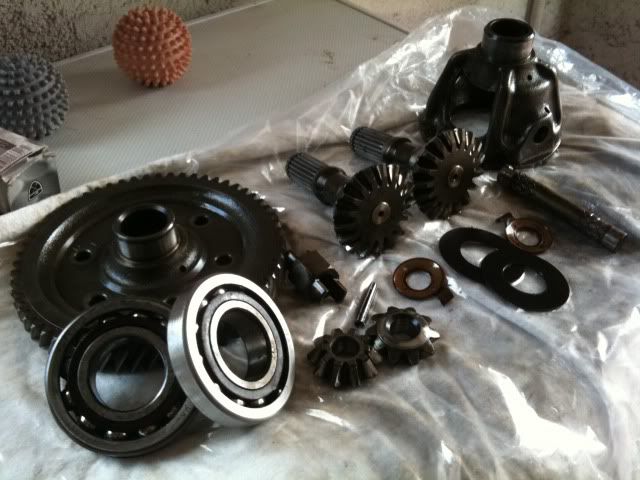
This is the stamp on the crown wheel which lets you know what your final drive ratio is, crown wheel 59 teeth, drive cog in box 19 teeth. 59 divided by 19 =
3.105. So the final drive ratio is 3.1-1 on this box.
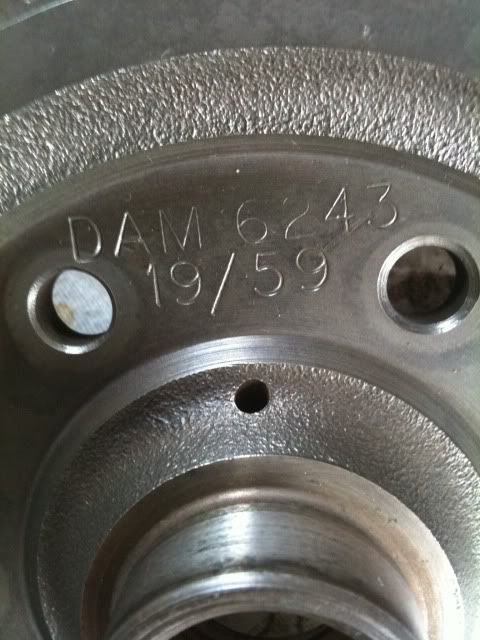
Now a quick swim in the degreaser a light coating of oil and its time for the photo shoot.
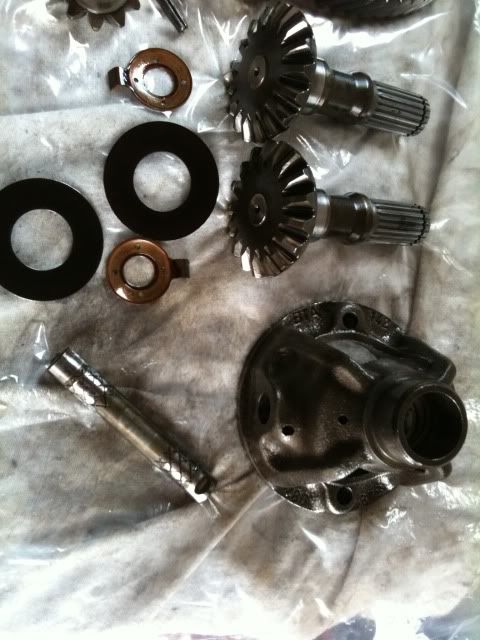
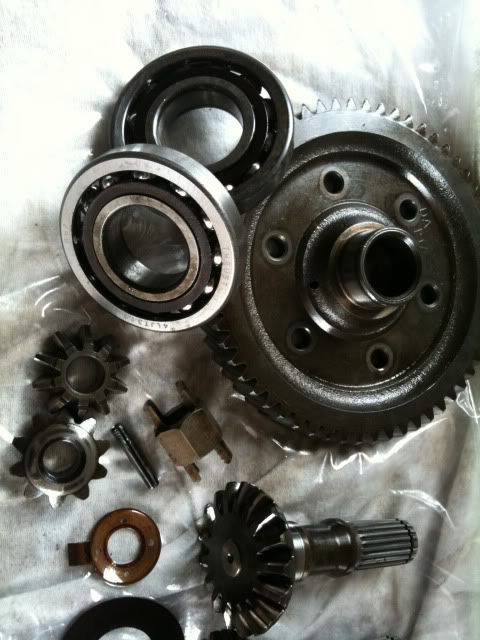
The uprated diff pin kit is on its way from Guessworks so i will put it all back togeher when it arrives.
Byeeee!!!
Edit.
A quick clarification, When I say "degreaser" What I really mean is an old buscuit tin filled with "GUNK" and a paint brush. ""It does the job people""
Edit Edit.
The calculation for the final drive ratio above is not something I just knew about, I found out by asking in the technical section and thought I would share. Sorry If I sounded like a bit of a "know it all". because I really dont.
Edited by AndyMiniMad., 27 February 2011 - 04:40 PM.