Thanks bud will do, cant wait to start, i have started a project engine build with a link to here might help others Andyminimad's idea i will try and upload as many pics as i can
If you are still there bud what do i seal new core plugs with and the oil way plugs
I normally use Loctite Bearing Lock to retain the core plugs, oil and water, although it's not strictly necessary. A drop of ordinary Loctite should work just as well really.
Make sure the oil galleries are scrupulously clean. Wash them out with paraffin and pull through bits of paraffin-soaked rag dragged by a piece of coat-hanger wire straightened out with a small hook formed on one end. Keep doing it until the rag is completely clean, then just wash through with brake & clutch cleaner.
Similarly make sure everything else is very clean before assembling.
It sounds as though the job is going well. Great.
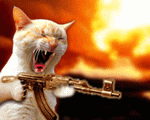
Stupid Dumb Question
#91
Posted 02 November 2011 - 02:11 PM
#92
Posted 02 November 2011 - 02:23 PM
For starters I always clean everything and wrap the parts in clean rag until they are needed. I generally clean with Jizer (or equivalent) which you wash off with a pressure hose, then dry and wash finally in Brake & Clutch Cleaner - get a 5 litre can of this.
Then start off with the crankshaft fitting. Fit the shells to the main bearing seats in the crank after making sure the seatings are free of any burrs or marks. I give the seating a light rub with 1200 grit wet & dry, then wipe clean. Fit the half-thrust bearings and, after coating the shells and thrusts with 'Engine Assembly Lube, lower the crank into place. Place the bearting shells into the main bearing caps, after lightly rubbing the surface of the caps and wiping clean, and fit them. Make sure the centre cap is fitted the correct way round - the simple check is to ensure that the numbers/letters cast into each cap all point the same way. Do the main bearing bolts up to 50 lb. ft. then check that the crank can be easily rotated by hand. Then measure the end float to ensure it's within tolerance - ideally 0.002" to 0.005". Once that's confirmed as correct, finally torque the main bearing bolts to 64 lb. ft.
Next step is the pistons, which you should have got press-fitted onto the rods by your machine shop. If you don't have one already, beg, borrow, buy or steal a piston ring compressor.
Let's do that stage as we go.
Good luck,
Peter
#93
Posted 02 November 2011 - 03:08 PM
Thanks bud machine shop is going to fit the pistons into the block for me , i did ask them to this will save me buying a ring compressor, this engine lube can i use whynns oil additive you know the thick oil in a tin just in case i cant get hold of anyIf you get stuck with the re-build sequence, come back, as I'm sure you will, and I'll list the assembly steps.
For starters I always clean everything and wrap the parts in clean rag until they are needed. I generally clean with Jizer (or equivalent) which you wash off with a pressure hose, then dry and wash finally in Brake & Clutch Cleaner - get a 5 litre can of this.
Then start off with the crankshaft fitting. Fit the shells to the main bearing seats in the crank after making sure the seatings are free of any burrs or marks. I give the seating a light rub with 1200 grit wet & dry, then wipe clean. Fit the half-thrust bearings and, after coating the shells and thrusts with 'Engine Assembly Lube, lower the crank into place. Place the bearting shells into the main bearing caps, after lightly rubbing the surface of the caps and wiping clean, and fit them. Make sure the centre cap is fitted the correct way round - the simple check is to ensure that the numbers/letters cast into each cap all point the same way. Do the main bearing bolts up to 50 lb. ft. then check that the crank can be easily rotated by hand. Then measure the end float to ensure it's within tolerance - ideally 0.002" to 0.005". Once that's confirmed as correct, finally torque the main bearing bolts to 64 lb. ft.
Next step is the pistons, which you should have got press-fitted onto the rods by your machine shop. If you don't have one already, beg, borrow, buy or steal a piston ring compressor.
Let's do that stage as we go.
Good luck,
Peter
lube
#94
Posted 02 November 2011 - 03:24 PM
If the machine shop are fitting the pistons into the bores, of course with rods attached, you must be careful to ensure that the pistons don't come out of the bores when you install the crank. You should place the block, face down, on a bench covered with clean cloth - an old towel is ideal. It can be a bit of a 'fiddle' to get the crank in with rods already in the block, but if you look at the task before you start you'll see what's involved. If using the same rod bolts, it's a good idea to fit new nuts. They are not expensive by themselves.
#95
Posted 02 November 2011 - 04:09 PM
thats fine bud need to do a little more shopping forgot to get a head gasket set, dont think i will get much for my birthday on the 5th pushing my luck with the wife now, you know the looks ha ha haMix the Wynns with some good 20w50 oil, about 50/50 ratio, and that will be just fine. It's just to ensure that there will be no bearing damage during initial engine rotation before the oil pressure comes up. We'll deal with first-time start-up later on.
If the machine shop are fitting the pistons into the bores, of course with rods attached, you must be careful to ensure that the pistons don't come out of the bores when you install the crank. You should place the block, face down, on a bench covered with clean cloth - an old towel is ideal. It can be a bit of a 'fiddle' to get the crank in with rods already in the block, but if you look at the task before you start you'll see what's involved. If using the same rod bolts, it's a good idea to fit new nuts. They are not expensive by themselves.
Edited by firefox, 02 November 2011 - 04:10 PM.
#96
Posted 02 November 2011 - 04:33 PM
#97
Posted 02 November 2011 - 06:17 PM
Ok, ill get my coat....
#98
Posted 02 November 2011 - 06:28 PM
I have got bloody fireworks all my life, yes i am 62 coming up never missed a year without them ha ha haBirthday on the 5th? Sounds like you will get a ROCKET!!! ha ha ha ha!!
Ok, ill get my coat....
but think of it this way, this is my gripe, other kids got fireworks it was my bloody birthday i never got presents just bloody firworks
and everybody was going ohhhhhh ahhhhhhhhhh isnt that one nice


Edited by firefox, 02 November 2011 - 06:30 PM.
#99
Posted 03 November 2011 - 10:41 PM
#100
Posted 03 November 2011 - 10:49 PM
The rebuild is on a project thread (1275 standard rebuild carried on from stupid dumb question)Deffo think this thread should get stickied! been toying with the idea of getting myself a 998 to strip down and rebuild to then swap with the 998 in my daily drive. All the advice has given me a bit of a spur in confidence! Thanks firefox for the "stupid question" and everyone else for the excellent advice!
glad it is some help to you bud
Edited by firefox, 03 November 2011 - 10:49 PM.
#101
Posted 03 November 2011 - 10:53 PM


#102
Posted 03 November 2011 - 10:54 PM
#103
Posted 03 November 2011 - 11:01 PM
Keep an eye on the other post bud not much on it yet i only got the block back today, i was a bit undecided to have a go but belive me you will get more satisfaction from DIY and save a few bobThis has been an amazing thread I'm taking mine off the road at Christmas for a full engine rebuild and this has given me the inspiration needed to do it myself instead of sending it off which I would rather not do! I've definitely subscribed and looking forward to see/ hear the end result!
NO a lot of bob
#104
Posted 03 November 2011 - 11:14 PM
Peter
#105
Posted 09 November 2011 - 04:47 PM
2 user(s) are reading this topic
0 members, 2 guests, 0 anonymous users