cheers pal appreciate it.
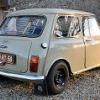
Project Checkmate....
#91
Posted 17 May 2013 - 07:54 PM
#92
Posted 21 May 2013 - 07:29 PM
Hello again,
So..........not much mini work again but im managing little bits here and there.
today i did a bit on the shocker mount as planned and have cut the outer plate ready for welding in another day.
So heres what i started with:
Cut back to see.... :
Made and magneticaly positioned repair piece:
Welded in :
And zinc primed:
So inner repair done, awiting spare time to weld in the other..
Cleaned up and primed radiator a good few days ago but wasnt enough for me to do an update on:
#94
Posted 21 May 2013 - 09:21 PM
It's ****. JOKING!!! Joking! (Don't kill me for that...)
How did you magnetically position it?? Or is that the magnet on the top right corner?
#95
Posted 21 May 2013 - 09:35 PM
It's ****. JOKING!!! Joking! (Don't kill me for that...)
How did you magnetically position it?? Or is that the magnet on the top right corner?
You'd better be
Haha yeah i is, think you're having a blonde moment there grace
Couldn't use my panel clamps as i wouldn't be able to get the thing off as theres a square pin on one side :/
#96
Posted 21 May 2013 - 10:20 PM
I won't say anything like that again!
shhh, hopefully nobody else will notice that I was
Ah right, well as long as it got the job done, not much of a problem right?
#97
Posted 21 May 2013 - 10:37 PM
I won't say anything like that again!
shhh, hopefully nobody else will notice that I was
Ah right, well as long as it got the job done, not much of a problem right?
You'd better not misses, family forum aswell so .....
Im sure they won't read what you have written so you're safe
Yeah it worked, i normaly use the magnet out of a car speaker i butchered for but panel clamps level out the repair piece to the shell so when i grind back the welds it more or less blends in.
#98
Posted 21 May 2013 - 10:47 PM
oh... Sorry small people!
so does the magnet not do that??
#99
Posted 21 May 2013 - 10:52 PM
oh... Sorry small people!
so does the magnet not do that??
Haha, doh!
Yes but not as id like, panel clamps put pressure either side as you tighten them up and force the panel up level, also something worth noting for everyone is that large magnets on small repairs (close to your welding) make the weld spatter so probably creates a crap/un-safe weld so best to avoid that .
#100
Posted 22 May 2013 - 06:40 PM
looking nice mate who needs magnets use your fingers?
#101
Posted 22 May 2013 - 07:31 PM
Hi tom, yeah this is what happens when you do though:
need to start wearing welding gloves again
On with the update.....
I,ve almost finished off welding the final shocker mount repair piece in:
90% welded in and zinc primed for tonight:
Then i re-found this:
Then this happened :
Then this happened too, the bonnet grew teeth :
Thankyou for viewing todays/a couple of hours work, next task i'l finish removing the bonnet lip then prime surface, start (finaly) on prepping the area for the flitch repair to be welded in.
Cheers again folks for your kind words
Cliff
#102
Posted 22 May 2013 - 07:37 PM
ouch! i bet that made you jump lol i had one land on my head running round like a headless chcken. trying to blow it. and lovelly work as allways.
#103
Posted 22 May 2013 - 07:42 PM
ouch! i bet that made you jump lol i had one land on my head running round like a headless chcken. trying to blow it. and lovelly work as allways.
Hahahaha that i'd pay to see tom
Just crouched down blowing my hand when it happens, think you can see a few more burns in that photo.
You must be joking ! my weldings getting worse , i'l need to do a second pass in areas
#104
Posted 22 May 2013 - 07:54 PM
beter then my welding i have bits or wire still attached lol and i need to get a mask and some gloves as i just hold it on and close my eyes for now lol
#105
Posted 22 May 2013 - 08:03 PM
beter then my welding i have bits or wire still attached lol and i need to get a mask and some gloves as i just hold it on and close my eyes for now lol
Haha yeah the lack of a mask might be an issue , whwt you're aiming for is to lead on/push forward the "puddle" which is the molten red part, at first its best to tack it in bit by bit until you get the correct balence between not blowing holes yet still getting a good weld, and also you're aiming for as little material to grind back post-welding.
Have a read up on welding techniques or pop over to the welders forum, a swirling motion as apposed to going down or up with your finger on the trigger is the correct method to use (There are others such as zig-zaging along but most seem to adopt the swirl).
0 user(s) are reading this topic
0 members, 0 guests, 0 anonymous users