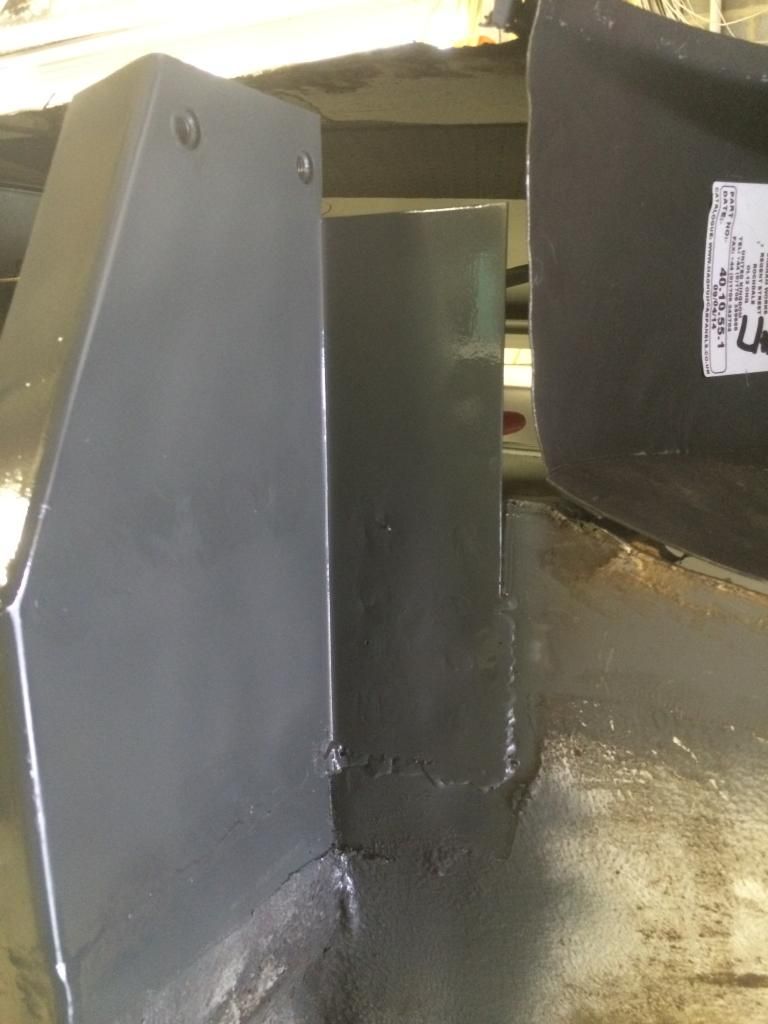
Next I decided to grab the bull by the horns and make a start on the boot floor. I offered the panel up and traced a line representing the maximum amount I could cut out. The corners were almost rotted through but elsewhere it's really quite good considering the rest of the car. So with this in mind I then marked a cutting line, trying to follow the contours of the panel and remembering the line where the patterned panel seems to fit best. Unfortunately I was so in grossed that I didn't get many photos.
Before I revved up the grinder I decided to unpick all the spot weld along the lip of the boot hinge panel. This turned out to be some of the easiest spots I've done so far on the car. I think largely due to two things, firstly a spot of oil on the tip of the drill bit every now and again, and secondly a tip I picked up reading Bens , recycling the back half of a mini posts, where he drills 3 spots then splits them, drills 3 more and so on. With an old chisel wedged in between the two panels I would drill and the panels virtually popped apart on their own, with just a tap moving the chisel along before drilling the next batch. Might just have been my lucky day, but I got that part done in next to no time.
So then I did a cut along the line I'd marked. With the bulk of the rear floor out the way I offered up the repair panel. I tucked it behind the existing floor where I could, I just had to cut a slit near the drivers side subframe stiffener bracket to allow it to fit. Difficult to explain but not really got a picture. I was then able to line the back edge up with the hinge panel and I fastened some bolts through the holes to hold it in place. Here's a picture of the sort of gaps that I'm gonna have to deal with to try and make it fit.
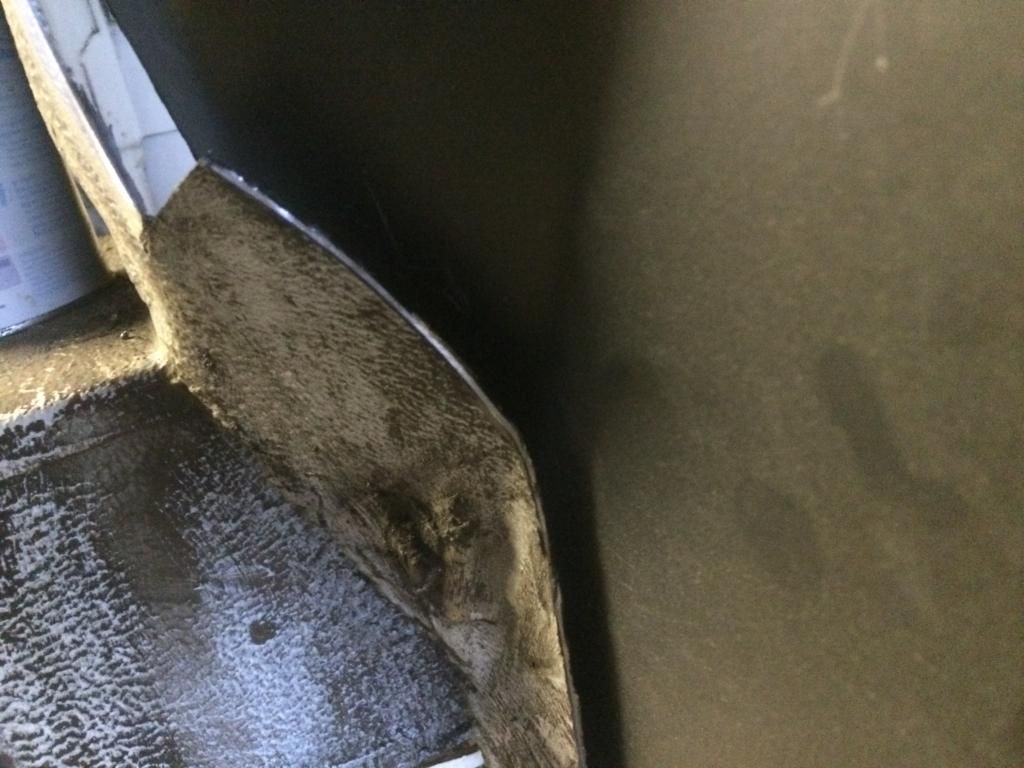
I know it's difficult to make out in the picture, but take my word for it - it's bad!!
The only way I could think to deal with the ill fitting panel was to make a few nip and tucks here and there, so a ran the cutting disc along one fold and tried to hammer the wheel well into the correct position. It then became clear the depth of the well was different between old and new. So then I cut a v shaped slit along the existing floor, brought the edges back together in the correct alignment and welded it up. Here's a close up of the work in question.
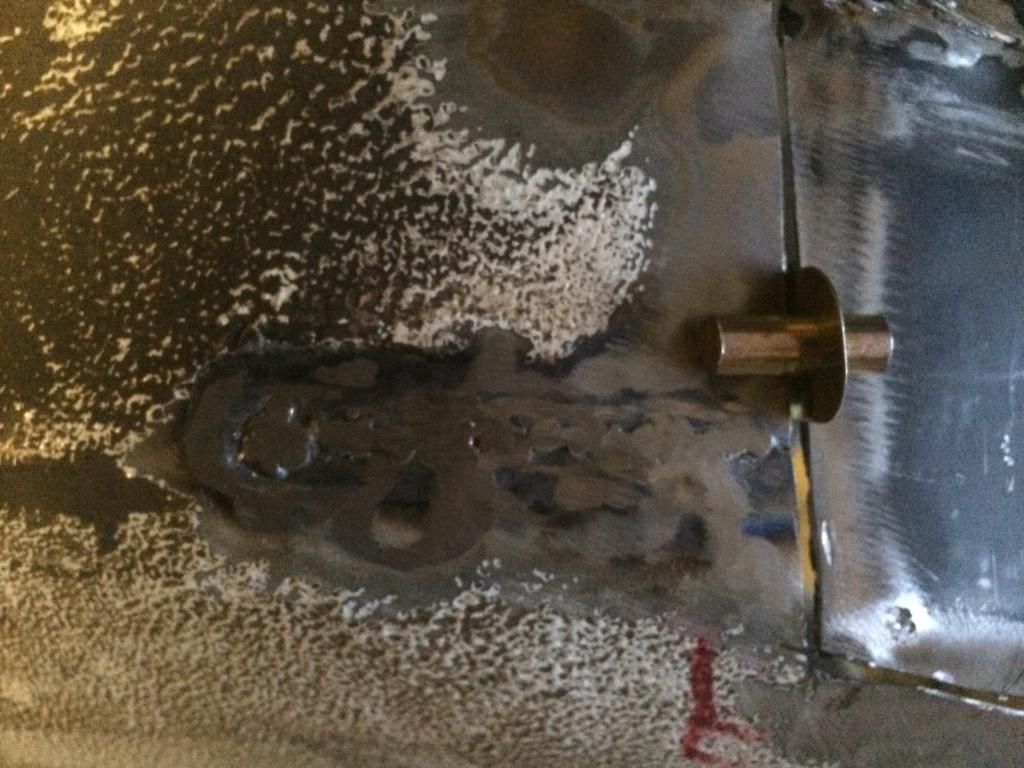
With some of the panel gaps closed up, and the old and new running slightly more true, I took the cutting disc and carefully went through both panels at once. This should leave me with a good line to butt weld. I used a plasma cutting disc, 1mm I think, to try and keep the gap minimal. I should be able to close the gap up a little more once I've got all the way across, with the play that I've got in the bolts holding the rear edge in position. This is how much I've done so far.
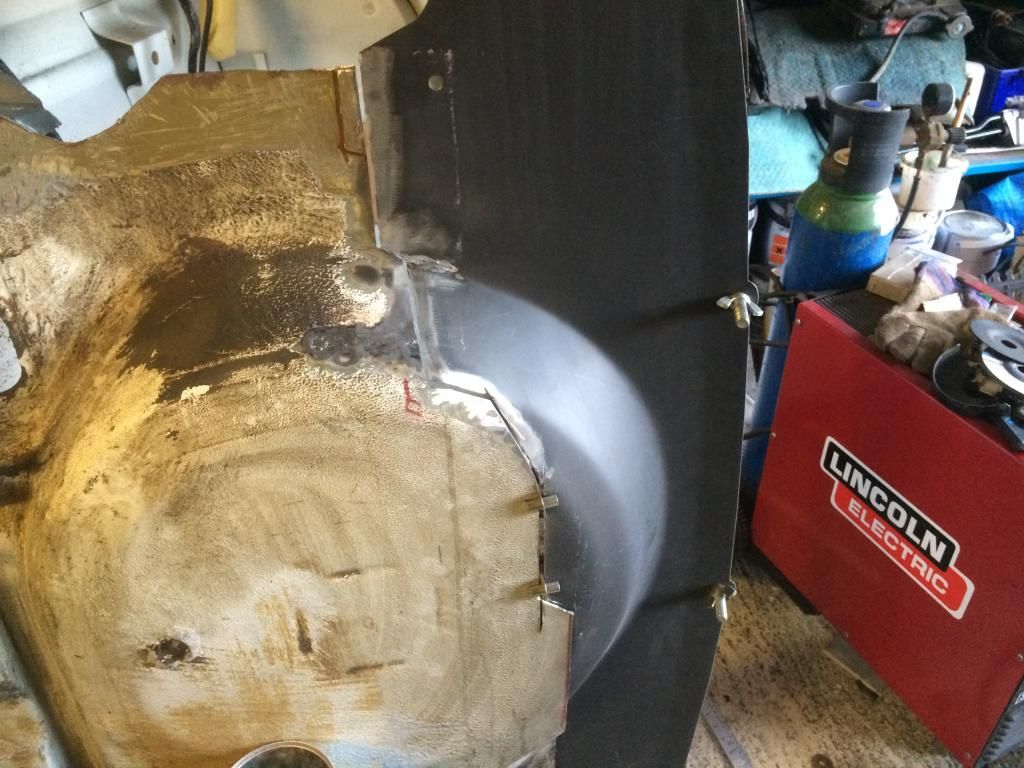
I'm contemplating welding the passenger side up and leaving the other side til I flip the car over. I'm just a bit worried that I may have forgotten to do something and regret it. This did lead me to realise I'm going to have to make a repair to the lip at both ends of the hinge panel. I don't think it's worth getting a new panel tho. So I made a card template and transferred it to metal with a haze of spray to leave a silhouette.
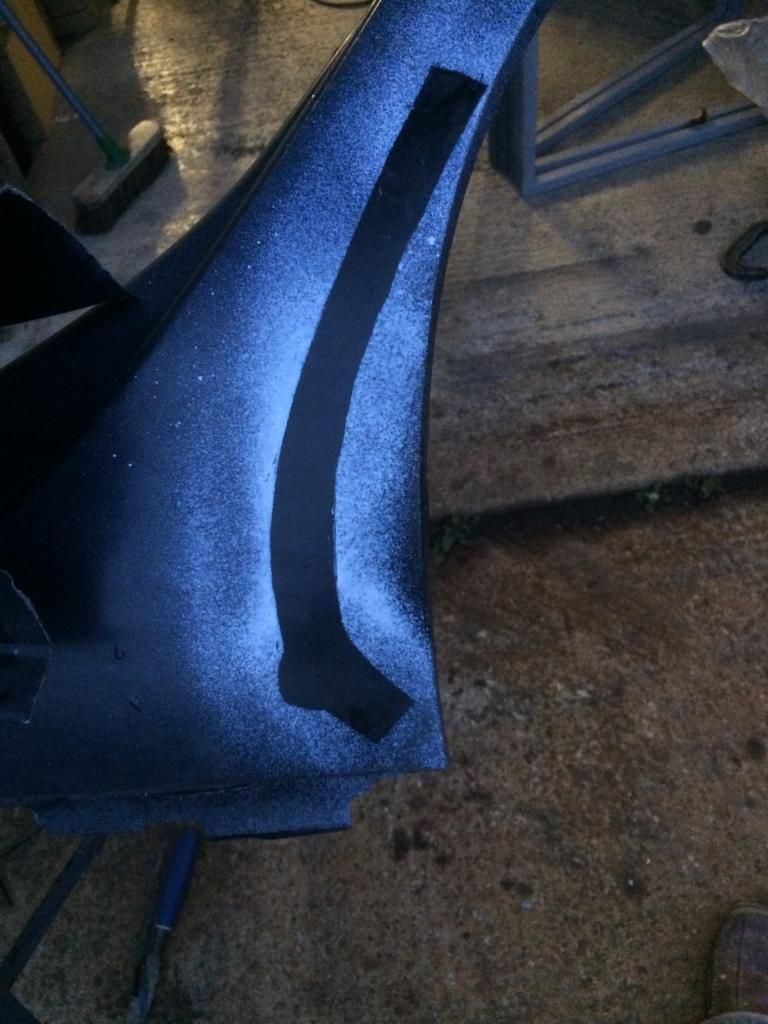
I had to leave it there for the night because it was late and I don't think the neighbours appreciate me using the grinder. Hopefully get a bit more done over the weekend.