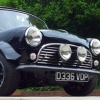
Welding And Sill Replacement
#16
Posted 09 April 2008 - 10:22 PM
But looking at the price of a disposible bottle - about £8 for about 7 mins use doesn't seem too bad to me for the amount of welding i expect i'll be doing. Alot of the welding i'll end up doing will be the odd small patch - I can't see me needing some sort of gas contract.
So how is argon better than co2? I've read that the gas is used to sheild the weld from oxidization - So what are the effects to the bead of weld when it comes into contact with oxygen?
#18
Posted 09 April 2008 - 10:30 PM
http://www.mig-weldi...welding-gas.htm
#19
Posted 09 April 2008 - 10:36 PM
Thanks for that link too. Looking at that, looks like a couple of the disposible argon/co2 mix bottles will be suitable for what i'll be doing.
Now about the wire. What are the different thicknesses for? Does this differ for the thickness of the metal your welding?
#20
Posted 09 April 2008 - 10:37 PM
#21
Posted 09 April 2008 - 10:42 PM
What about the wire material itself? The ones i've seen are described as mild steel - Is that what i need?
i.e. If i want 0.6 then is this what i need: http://www.halfords....tegoryId_128815
Also just so i can get an idea of cost again - How long will a 700g roll of wire like that last me? I guess that'll depend on how thick im putting on the bead of weld and things doesn't it?
#22
Posted 09 April 2008 - 10:46 PM
I have no idea how long 700g will last as I use 15kg reels!!!
If you only use the weld infrequently then small reels are best as welding wire "goes off" after 12 months. it can also go rusty which is fatal!!
Yes you need mild steel wire
Screwfix also sell it cheaper!!
#23
Posted 09 April 2008 - 11:03 PM
Just had a look through the screwfix website - Can't find anything apart from welders - Pretty poor search function on the site i guess. According to the branch locator theres one a 10 minute drive from me so won't hurt for a trip down there. You don't have to be some sort of trade member to buy from there do you?
Just looked on the machine mart site - They do a 5kg real of 0.6 mild steel wire for £15 - So that seems nice and cheap and 600g co2/argon mix disposible gas bottles are a tenner.
One last thing i need to ask about - Voltage. I have no idea what to even ask about this but i know its a pretty important factor i need to know about.
#24
Posted 09 April 2008 - 11:21 PM
For car bodywork you will need a welder that goes down to 30amps. Some clarkes will go down to 25amps, however 30 is the norm.
#25
Posted 09 April 2008 - 11:41 PM

#26
Posted 10 April 2008 - 11:56 AM
'Clean up the surrounding metal, hold/clamp/secure new panel in place, tack the sill into place with small blobs of welded dotted every... say 6 inches?, then once thats done do i continue adding a full bead of weld all the way around the sill in small sections? Then clean up the welding with a grinding disk on the grinder?'
Have i missed anything there?
#27
Posted 10 April 2008 - 01:16 PM
Cheers
David
Edited by R1mini, 10 April 2008 - 01:17 PM.
#28
Posted 10 April 2008 - 07:11 PM
But doing it this won't it leave some parts of the sill pretty open to the elements? Replacing sills isn't i job i want to do every 6 months - I'd rather them be watertight.
#29
Posted 10 April 2008 - 07:20 PM
#30
Posted 10 April 2008 - 07:30 PM
0 user(s) are reading this topic
0 members, 0 guests, 0 anonymous users