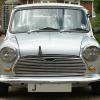
Fern...
#166
Posted 04 February 2012 - 10:05 PM
#167
Posted 05 February 2012 - 07:06 AM
#168
Posted 07 February 2012 - 08:30 PM
#169
Posted 08 February 2012 - 11:35 PM
Toyota Gunmetal, code is 6N0

#170
Posted 16 February 2012 - 07:00 AM
Drivers Before:

Passengers Before:

Drivers bolster:

Once I'm ready to reinstall the interior I'll make up some new brackets to fit the mini seat runners to them so they'll fit straight in.
#171
Posted 24 February 2012 - 10:16 PM

Previous owner had done a bad job & a brick started pushing it's way out through the plaster. All rebricked properly now, just needs a skimm of plaster & then we can wall paper.
Back to the car then . . . I managed to get the repair section to the front moved on, I made the panel longer than it needs to be so I can cut & bend it to the right shape once I have the inner sill repaired & know where everything goes again. Lesson learned, don't cut too much out at once or I won't have a decent reference point. It was a bit difficult to get inside the crossmember but I gave it a quick wire brush then pumped it with zinc primer, which I will cover with Rustoleum direct to rust metal paint with a brush next session. I also managed to borrow a joggler so now I dont have to drill the holes for spot welding, it's brilliant & quick! I used it on the new tab I created for the crossmember as the old one was cut out with the rust. So next time I will be tacking in the inner sill & making sure it, the outer sill & flitch all match up correctly before more welding.



#172
Posted 27 February 2012 - 06:18 PM
#173
Posted 02 March 2012 - 06:43 AM

The idea is to recess the panel where the number plate goes enough to be able to put lights in (from a VW golf) & also to have them hidden under a lip whilst still keeping a fairly smooth look to the boot lid. I've welded up the old number plate light mounting holes too.
First I measured it all up & marked centerlines etc then figured out where everything will go. I made relief cuts down the sides & removed the bracing in the way at the back.


I then cut the center piece in two, this will have a section added in once I have it all bent to the angles I need.

Final pic is as it stands at the moment where I just need to panel beat the bottom section enough to bend it inwards & flatten it out to meet the top section. I'll have to take my time welding so I don't distort the panels

The sides of the number plate recess will be getting smoothed off as well but will probably cut them out & replate with flat metal.
Edited by Brams96, 02 March 2012 - 06:45 AM.
#174
Posted 02 March 2012 - 07:09 AM
#175
Posted 02 March 2012 - 07:26 AM
#176
Posted 07 March 2012 - 06:37 PM
I plan on making the side repair pieces bend down the side so will try making them out of 1 piece, which again will be a pain as they will need to have a slight curve to follow the boot line. More bashing & swearing. Once this piece is welded in I'll finish the side pieces then put the lip accross the top of the recess. I will need to weld everything really slowly so I dont warp the panels with the heat from welding. I might also get some lead so I can try lead loading on the boot to get the hang of it before I attempt the car itself. There are a few small dents from panel beating I'd like to smooth out without filler if I can help it & the lip will need doing too.
Pics time. . .



Edited by Brams96, 07 March 2012 - 06:40 PM.
#177
Posted 12 March 2012 - 06:58 AM

Then had to make this fit

Problem was the anlged part needed to curve along the black line while the other part stayed straight & after about an hour of trying to shrink & stretch the metal to get the right shape it just wouldn't work so it went in the bin! I will attempt the next piece by making relief cuts along the edge & welding them up, a bit of a longer process but will give better results in the end.
Edited by Brams96, 12 March 2012 - 07:00 AM.
#178
Posted 13 March 2012 - 06:16 AM
Got out to the garage for a couple of hours last night & fabricated a piece for the repair to one side. I started by cutting out the piece from cardboard then transfered it to metal slightly wider than I needed & then made 5 cuts to the bend line, bent each piece over & then trimmed off the extra metal. After this I made sure everything fit & welded it together by clamping 2 pieces together at a time until it was all done, making sure I checked the fit after each section was completed. It's a lot of welding, changing masks, grinding & rechecking but I think it'll be worth it in the end, also it takes time to let the metal cool so nothing warps (lots of tack welds).
I still need to flatten off the welds & tidy the front up, trim the excess metal at the back then I can make up the other side. Once it's all done I can try lead loading all the edges/joints. The hard part is welding in the corners of the right angles as the weld tends to lump up before you can reach in there, I'll have to tidy it up with the dremel I guess.
As it stands at the mo...



Edited by Brams96, 13 March 2012 - 06:20 AM.
#179
Posted 25 March 2012 - 03:40 AM


I've also seam sealed it as much as I can & where I can reach & those I can't I'll be Waxoyling them. Still to do is cut & mount the lights & then make the hinges, I'm still in 2 minds about this so I haven't filled the hinge or boot lock holes yet.
#180
Posted 30 March 2012 - 05:13 AM

I also had to weld the small repair section I'd already made to it & now the whole thing fits as one & a lot better than the 3 pieces I would have had to use.

After a bit of proding, I also got round to stripping the rear subframe which has been sitting on our deck since I stripped the car. It's a complete write off with holes & more rust than good metal. I stripped down the radius arms too & found both brake cylinders had 1 seized piston, hand brake quadrants & adjuster nuts. Nothing a bit of heat, penetrating spray & persuasion didn't fix!

Edited by Brams96, 30 March 2012 - 05:16 AM.
1 user(s) are reading this topic
0 members, 1 guests, 0 anonymous users