Edited by miniman92, 25 January 2012 - 09:30 AM.
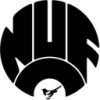
Engine Strip Down And Rebuild With Lots Of Confusion :d
#151
Posted 25 January 2012 - 09:29 AM
#152
Posted 25 January 2012 - 10:09 AM
It has no horizontal movement on the crank with thrusts in might put the old one's back in just to compare the difference got tired and frustrated last night so will try again after work will post piccies cheers for you help
#153
Posted 25 January 2012 - 10:16 AM
#155
Posted 25 January 2012 - 10:51 AM
If I get one can I check the float with the crank and pistons fully assembled?
If so I'll just spend some time modifying and painting the timing cover and reassembling the head.
#156
Posted 25 January 2012 - 12:56 PM
It won't take you long to re-fit the pistons later on, it's worth doing it right rather than cutting corners.
Like you say....... Just take your time with it and spend some time prepping other bits while your waiting for the dti. You could always clean up your transfer case.... fit it to the gearbox and then measure your idler gear end float etc?
Ash
Edited by miniman92, 25 January 2012 - 12:56 PM.
#157
Posted 25 January 2012 - 01:14 PM
Cheers for your help Ash
#158
Posted 26 January 2012 - 05:42 PM

when i was disconnecting the mind blank, tube/bar that the connects gearstick to diff on gearbox at the gearbox side it meets a shoulder union joint with two roll pins securing your meant to tap one out to release the bar and seperate. which i managed eventually one problem the drift i used was just too small and kind of snapped inside the roll pin making a perfect fit. Couldn't get it free when i had the engine out so figured just cut it down to the shoulder and bobs your uncle.... However i need to get the shoulder off to fit the minispares oil leak quick fix kit.... any ideas people tried drilling, heat and whacking kind off need to get the rod that goes into the diff free to put it into a vice to get the right angle and weight. however cant get the diff housing past the shoulder.....

#159
Posted 26 January 2012 - 07:45 PM
Have you not got the correct roll pin drift tool?
Try using a suitably sized drill bit (about 7-8mm) and put the chuck end against the roll pin and smack the other end with a good sized hammer. WD40 helps too! PS.... watch out for sparks when you hit the drill bit!
#160
Posted 26 January 2012 - 09:41 PM
#161
Posted 26 January 2012 - 09:49 PM
#162
Posted 27 January 2012 - 09:18 AM
#163
Posted 27 January 2012 - 02:30 PM
if all else fails........disc cutter, chisel and hammer get most things off, then you wiill have to buy a new connecting peice
#164
Posted 27 January 2012 - 03:36 PM
#165
Posted 27 January 2012 - 04:53 PM
Cheers Andy that is exactly what has been happening I put the Old thrusts in and it was the same just but nervous I get it wrong and the engine seizes up.
1 user(s) are reading this topic
0 members, 1 guests, 0 anonymous users